To understand finishing plastic parts, you must first understand the process that goes behind creating the plastics. There are many ways to machine plastics. When you have a plastic that has been machined, it will come at a specific gradient of roughness to smoothness, which will determine how much and what kind of finishing it will require. Check out our guide to surface finishing on machined plastic parts to broaden your understanding of how plastics are finished.
Surface Roughness
Determining the surface roughness is the first step that should occur after plastic parts are machined. This is done through measurements by using a unit known as Ra. The Ra is calculated by taking a deviation from the mean of the surface plane and then applying it in microinches, thus determining the roughness.
A standard is typically used to give a rough idea of where machined parts reside. For example, a cast-iron skillet has a Ra of roughly 2,000, whereas the surface of the Hubble Space Telescope has a Ra of 0—and machined plastic parts fall somewhere in the middle. Using this standard is yet another way to understand and determine the roughness of machined surfaces.
Smoother Surfaces
There are multiple ways to achieve the desired result of smooth surfaces on machined parts. The first factor you should always consider is what machining process the piece went through before finishing. The finishing process that the piece goes through could greatly determine the outcome of the piece.
The quicker a part is machined, the less finishing it will take because the parts are being pumped out at a faster rate. This allows more finesse to be applied toward the part, as the processing takes more time, which results in a smoother, finer piece.
In general, faster-machined parts will have a Ra of somewhere around 65 to 60, and this is normally accepted as a smooth finish. However, there are other alternative methods that can achieve smoother finishes.
The problem with having a Ra with a range like this is that the plastic part may not look rough to the naked eye, but it may still have rough cuts and burs in places that should be smooth. This can prove to be problematic in manufacturing.
Over time, having rough cuts and burs causes a whole host of problems, including corrosion and the wearing of gears and other parts. When you achieve a smoother finish, it results in a tighter bond, which is important in creating seals and fastening parts together tightly for cohesion during construction. If you take the proper amount of time to machine plastic parts, you can achieve a Ra of around 32 which is considerably smoother.
Post-Process Finishing
There is also a secondary level of finishing that occurs in plastics machining. There are generally two different avenues of finishing when it comes to machined surfaces, and that’s through either graining or lapping. In both processes, the piece is moved against an ordered series of finer gradient textures to achieve different levels of abrasion. The process is repeated until achieving the desired level of finish. The product can then be sent out for shipping.
The real difference between these two methods is the finish that they provide. Graining typically finishes with a Ra of around 4 to 32, whereas lapping finishes with a Ra of around 2 to 16 on average. So, the type of material that you are using and what the piece will be used for will mean the difference of whether you choose to use graining or lapping as a finishing method.
There are other alternative methods that can be used for finer finishes with plastics as well. Bead blasting is a method seldomly used due to its destructive force and nature. While it may work extremely well, the bead blasting method always runs the risk of your parts getting damaged in the finishing process. So, this may be a process that you need to carefully consider before selecting.
If you’re going for a more matte look in your finish and you want to avoid any sheer or sheen in your product, then you might opt for injection molding. This will give you a perfect product every time, as it involves the part being processed through a mold, where it will be in a perfect environment and machined to the exact specifications. An exceptional means of production worth every second.
If shine is something that you’re after, then you might want to try your hand at wet sanding, which is typically used in metal finishing applications. Just like lapping and graining, a progressively finer grit is applied until a perfect finish is achieved for your specific product. This process can prove to be very laborious, but it’s worth it in the end.
The final method of post-process finishing that is applied in more specific situations is the process of flame polishing. Through this method, just enough heat is applied to level out all the elevated spots and dips that are uneven with the plane that comes with machining leftover from other processing techniques. This method isn’t as widely used but is an effective way of quickly smoothing over the outside of plastic pieces to level out the surface for a nice finish and uniformity across the surface.
Final Thoughts
Plastics all serve different purposes, which is why they all require different levels of finishes. Some plastics require no finish after being machined. Knowing the roughness factors and understanding when certain parts need more finishing gives you a greater insight into how plastics work and how we use them.
The finish of the product determines its lifecycle various uses. So, it’s important that the correct finish is used for every part assembled in plastic manufacturing. Another useful consideration is the lifecycle of plastics, which can also determine the type of finish required.
Not all plastics are made the same, therefore some can be recycled, while others can’t. This alone highlights the importance of the precision of various plastics finishes. This is where precision plastic machining comes into play, as the major contender above all other machining methods.
There are many ways and alternatives to plastic fabrication, just like there are various plastic finishing processes. Hopefully, this guide to surface finishing on machined plastic parts has helped you gain a better understanding of how the process works.
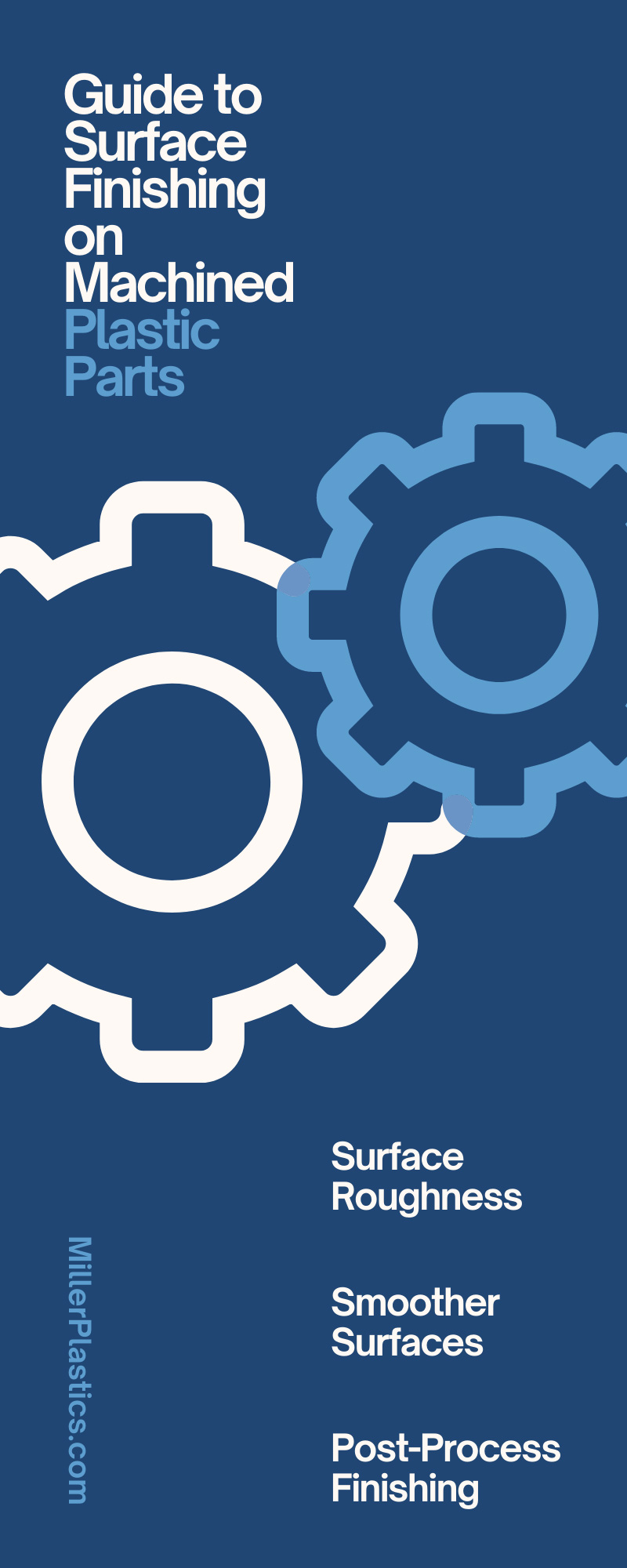