When selecting a storage or process tank for industrial applications, the material affects efficiency, longevity, and cost-effectiveness. Polypropylene tanks are top contenders among the many options available. This material has a unique combination of features that make it superior to polyethylene, fiberglass, PVC, and high-density polyethylene (HDPE) in various industrial settings. Keep reading to learn more about how polypropylene tanks outperform other plastic options.
Understanding Polypropylene as a Material
Polypropylene is a lightweight yet strong thermoplastic polymer. This material can withstand challenging environments and exhibits high structural stability and thermal resistance. Polypropylene also has an inherent ability to resist a wide range of chemicals, making it suitable for chemical processing, wastewater treatment, and food and beverage manufacturing.
Due to its molecular structure, polypropylene with a higher melting point than other plastics, such as polyethylene and HDPE, making it capable of handling elevated temperatures without deforming. Thanks to its thermoplastic versatility, polypropylene tanks can meet the specifications of industrial applications.
Strength and Durability
Polypropylene consistently outperforms polyethylene and HDPE in terms of strength and durability. While polyethylene is useful forplastic chemical tanksdue to its affordable cost, it falls short in applications requiring tensile strength or impact resistance. By contrast, polypropylene can maintain its structural integrity under great physical stress.
Fiberglass tanks offer marginally higher strength but are subject to brittleness and cracking over time, especially when exposed to fluctuating temperatures. Polypropylene tanks, on the other hand, resist impact and wear while exhibiting greater flexibility and preventing cracks from developing. With this balance of strength and adaptability, polypropylene tanks require less frequent maintenance than fiberglass models.
Superior Chemical Resistance
Material compatibility determines the lifespan of storage tanks holding aggressive chemicals. Polypropylene offers better chemical resistance to acids, alkalines, and solvents than PVC, polyethylene, and HDPE. While chemically resistant, PVC can become brittle under prolonged UV exposure, limiting its applications in outdoor settings where polypropylene shines.
Additionally, HDPE handles various chemicals well but deteriorates faster than polypropylene when exposed to oxidizing agents or high temperatures. If you use corrosive chemicals, you’ll find that polypropylene tanks deliver outstanding protection with minimal degradation over time.
Temperature Tolerance
Industrial processes may involve fluctuating or elevated temperatures, and polypropylene has heat resistance. Polyethylene, HDPE, and PVC tanks are common in medium-temperature settings; however, these materials deform or lose shape at higher temperatures.
Polypropylene maintains mechanical stability at temperatures up to 200 degrees Fahrenheit (93 degrees Celsius) and tolerates short-term increases without deteriorating. Conversely, PVC softens considerably under high heat, and HDPE begins to deform well below polypropylene’s limits. Polypropylene is ideal for high-temperature chemical mixing or sterilization because it maintains reliability in high temperatures.
Lightweight yet High-Performance
Fiberglass tanks offer strength, but their heavy weight makes them cumbersome and difficult to install. Polypropylene provides a much lighter alternative without sacrificing durability. This lightweight nature makes polypropylene tanks easier to transport, handle, and install on-site, reducing labor costs and installation times.
Polypropylene performs better than HDPE and polyethylene tanks for its weight. With its advantageous strength-to-weight ratio, engineers can create tanks in larger sizes or customized geometries while preserving structural integrity. They benefit from reduced logistical complexity without compromising essential performance metrics.
Extended Lifespan
Few materials resist environmental and operational wear as well as polypropylene. Polyethylene and PVC tanks have shorter lifespans due to UV exposure or chemical interactions. Meanwhile, polypropylene resists premature aging, even in highly corrosive or outdoor environments.
Though durable, HDPE tanks degrade faster under cyclic loads or chemical stress cracking than polypropylene. Fiberglass tanks face concerns around resin wear or UV degradation over time. Polypropylene’s lifespan often exceeds expectations under the same conditions, reducing long-term replacement expenses for industrial managers.
Cost Effectiveness in the Long Run
Although polypropylene tanks may have a higher initial investment than PVC or polyethylene options, they deliver cost savings over their operational lifespan. Their reduced maintenance requirements, resistance to damage, and extended longevity all contribute to lower total ownership costs.
Fiberglass tanks have high upfront and maintenance costs due to their specialized manufacturing processes. Conversely, polypropylene balances affordability and resilience; you’ll get a high ROI without sacrificing quality.
Environmental Compatibility
Sustainability is a priority for many business leaders, and polypropylene excels in this regard. Fiberglass tanks require energy-intensive processes for manufacturing, and it’s difficult to recycle. Polypropylene, on the other hand, is fully recyclable and has a smaller carbon footprint.
Many polyethylene tanks contain additives that can leach into the environment over time. Polypropylene is inherently stable, so no harmful substances will enter the environment. Business leaders striving for eco-conscious practices lean toward polypropylene as an environmentally sustainable material for storage tanks.
Versatility of Design
Polypropylene enables greater flexibility in tank design compared to other plastics. Manufacturers can easily fabricate and weld polypropylene to build custom tanks that meet different industry requirements. In contrast, fiberglass tanks require molds or specialized labor during production, which limits their versatility.
Polyethylene and HDPE also offer limited design adaptability due to the challenges associated with heat-shaping these materials. On the other hand, engineers can incorporate internal baffles, fittings, or sectional compartments into polypropylene without compromising material performance.
Health and Safety Compliance
Adherence to strict health and safety standards is crucial for professionals in food processing or pharmaceutical production. Polypropylene meets the Food and Drug Administration (FDA) and the National Science Foundation (NSF) standards for food contact applications, making it an optimal choice for tank manufacturing.
While HDPE and polyethylene also meet safety certifications, polypropylene’s superior chemical and thermal stability often make it great for use in clean manufacturing environments. Fiberglass is not ideal for applications requiring strict health compliance because it can release harmful fibers or chemical irritants.
An Investment in Reliability
Polypropylene tanks outperform other plastic options, underscoring their value in many industries. Engineers, industrial managers, and business owners who prioritize durability, chemical resistance, and design adaptability can rely on these tanks for long-term operations.
If you’re looking to optimize your processes, you need polypropylene tanks. Equip your business to succeed in challenging industrial applications, and shop for high-quality custom polypropylene tanks atMiller Plastic Products. Contact us today to get started on your custom solution.
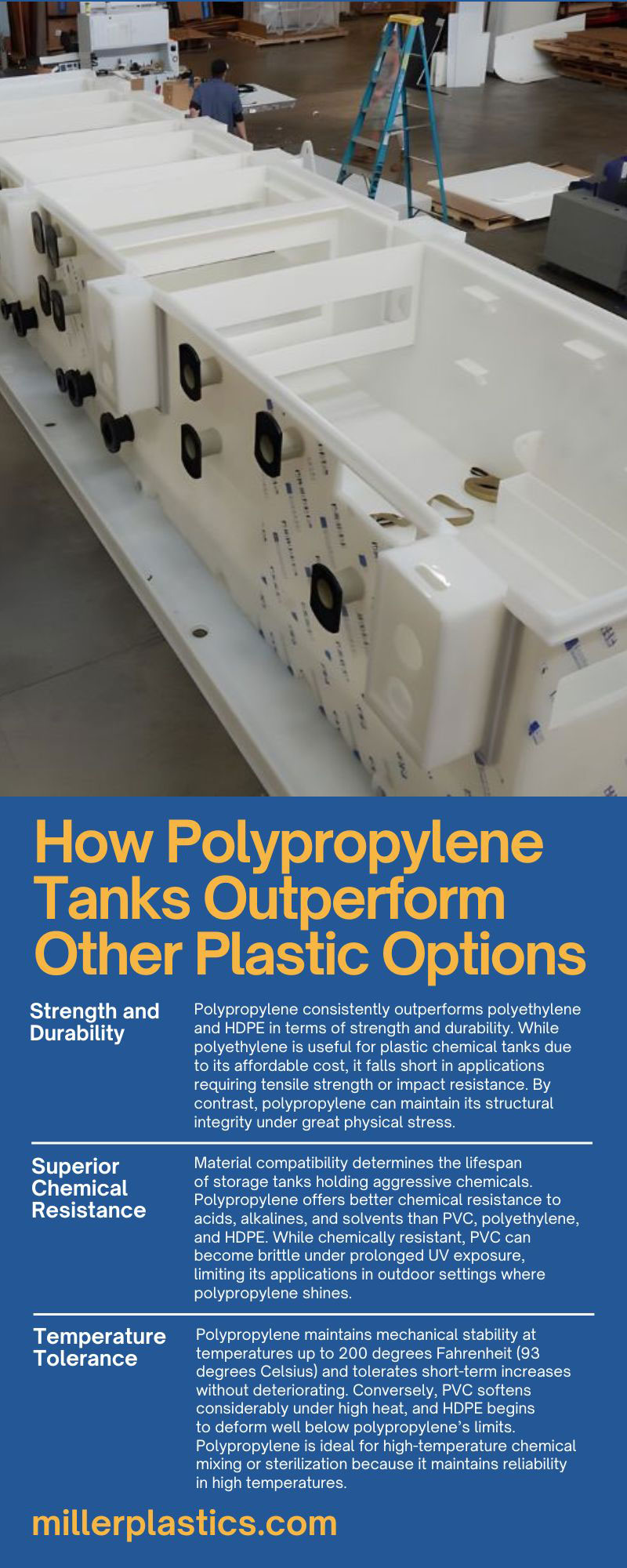