Making custom tanks is a big job. When you need a container of that size, you want to be confident that you have the right material, measurements, design, and manufacturer. You can’t afford to make a mistake on this scale. But by learning how plastic tanks are manufactured, you’ll know how to look for quality from the beginning to the end of the process.
Why Plastic for Tanks?
Plastic tanks are so versatile because they’re less likely to react with what’s inside. Many chemicals will clash with and corrode metal tanks, and plastic makes often more financial sense. Plus, there are plenty of different kinds to choose from, with variable characteristics for your project. Plastic is lightweight, strong, and is more flexible design-wise than other options. Really, the only factors that limit plastic tanks are the most extreme temperatures and the chemical resistance chart. Once they’re in use, plastic tanks are much more easily repaired than those made from metal and ceramics.
Who Uses Them Now?
Once you look into it, you’ll come to realize that pretty much everyone needs a plastic tank for something. Liquids need to be contained and transported in endless industries, including:
- Agriculture
- Petrochemical
- Gas
- Oil
- Water treatment
- Chemical
- Food
- Beverage
- Recycling
- Manufacturing
- Electroplating
- Biomedical
- Pharmaceutical
- Semiconductor
What’s Their History?
Tanks in general, of course, have been in use for thousands of years, and have been made of wood, stone, and ceramics. As far back as 3000 BC, the Indus Valley Civilization in South Asia used tanks for storing water and grain.
By comparison, plastic tanks are very young—but often far preferable to the traditional materials. Plastics were created in the 1800s, but the technology for tank fabrication didn’t arrive until the 1960s. That’s when engineers developed new processes for making large hollow containers.
The first plastic tanks were constructed with low-density polyethylene. Since then, though, the methods and plastic compounds have diversified. Now, with the right combination of material, technique, and manufacturer, you can produce a more effective tank than ever before.
How Are They Made?
New methods for manufacturing are always being developed, but these are two of the most common for plastic tanks:
Injection Molding
Smaller tanks are ideal for this technique. The molds are usually made from steel and have cavities where the part will be formed. Melted plastic is injected into the mold in the shape of the cavity. After the mold has cooled, the part is ejected by pins. It’s not unlike using a Jell-O mold.
Rotational Molding
Also called “rotomolding,” this process is better suited for large, one-piece tanks. The heated liquid inside the mold is rotated to coat the inside of even more complex shapes. It uses centrifugal force to keep the walls at a consistent thickness.
What Materials Are Best?
Every plastic has its own set of characteristics that will make it the perfect choice for your tank—or just another also-ran. It’s best to start with the chemical resistance chart so you can rule out any varieties that can’t hold up to your liquid. The most commonly used plastics include:
Polyethylene
This is the most widely used plastic in the world, and for a good reason. It has a continuous working temperature of 180 degrees Fahrenheit, but actually comes in three grades:
- Low-Density
- High-Density
- Ultra-High Molecular Weight
Polyethylene is a premier thermoplastic that can stand up to both chemical and physical attack. It can even be used for food storage. Its other benefits include:
- Superior mechanical properties
- High stiffness
- Excellent low-temperature impact strength
- Impressive environmental stress crack resistance
Polypropylene
This is the second most widely used plastic, and is often called the “steel” of plastics. It has a working temperature of 200 degrees Fahrenheit. Some of its advantages for tank construction include:
- Superior heat deflection properties
- High degree of tensile strength
- A semi-crystalline structure that makes it particularly resistant to chemical damage
- Strong and stable
- Excellent fabrication abilities
- Inexpensive
- Good availability
How Are They Customized?
You’ve probably found that the containment unit you need doesn’t exist—yet. That’s why you’re learning how plastic tanks are manufactured, and you want to know what your options are. Well, the sky’s the limit—if you’ve got a ladder that high. Miller Plastics has constructed holding tanks that range from less than one cubic foot to more than 50 feet long. Do you need to store 15 gallons—or 16,000 gallons? It can be done. You can customize the following tank properties:
- Size
- Shape
- Configuration
- Dimensions
- Orientation
- Material
- Color
In addition, many customers have asked for functional customization like translucent tank walls so they can monitor contents.
How Do You Judge Quality?
You’ll be the one to answer that after your custom tank is manufactured. But here are a few ways that you can upgrade your tank, as well as measure it against standards.
Extra Treatments
- Finite Element Analysis: FEA maximizes performance and ensures minimal bowing.
- Annealing: This heating-and-cooling process strengthens the tank.
- Bands and Baffles: If your tank is self-supporting, we can reinforce it with plastic-encapsulated bands. Another option is utilizing internal baffles that can minimize sidewall bowing.
Official Standards
Your industry will have its own set of metrics to guarantee the safety and performance of your tank. A couple of possibilities include:
- The American Society for Testing and Materials (ASTM)
- The American Petroleum Institute (API)
- The National Fire Protection Association (NFPA)
- Underwriters Laboratories (UL)
- American National Standards Institute (ANSI)
- American Society of Mechanical Engineers (ASME)
Your Own Standards
The harsher the chemical you’ll be storing, the more essential it is that your tank is up to the job. It’s up to you to insist on the best quality, by your own definition. If you’re anything like us at Miller Plastics, you’ll require:
- The latest CNC equipment for cutting
- Welding that’s held to the strict specifications of Germany’s nonprofit DVS
- Consistent precision, reliable performance, and a smooth finish
- 100 percent virgin, American-made materials
Now that you know what kind of service you deserve from your plastic tank manufacturers, Miller Plastics is here to answer any questions you have that are specific to your project. We have more than 50 years of experience making single tanks, integrated systems, and more. Contact us for details or to get a quote.
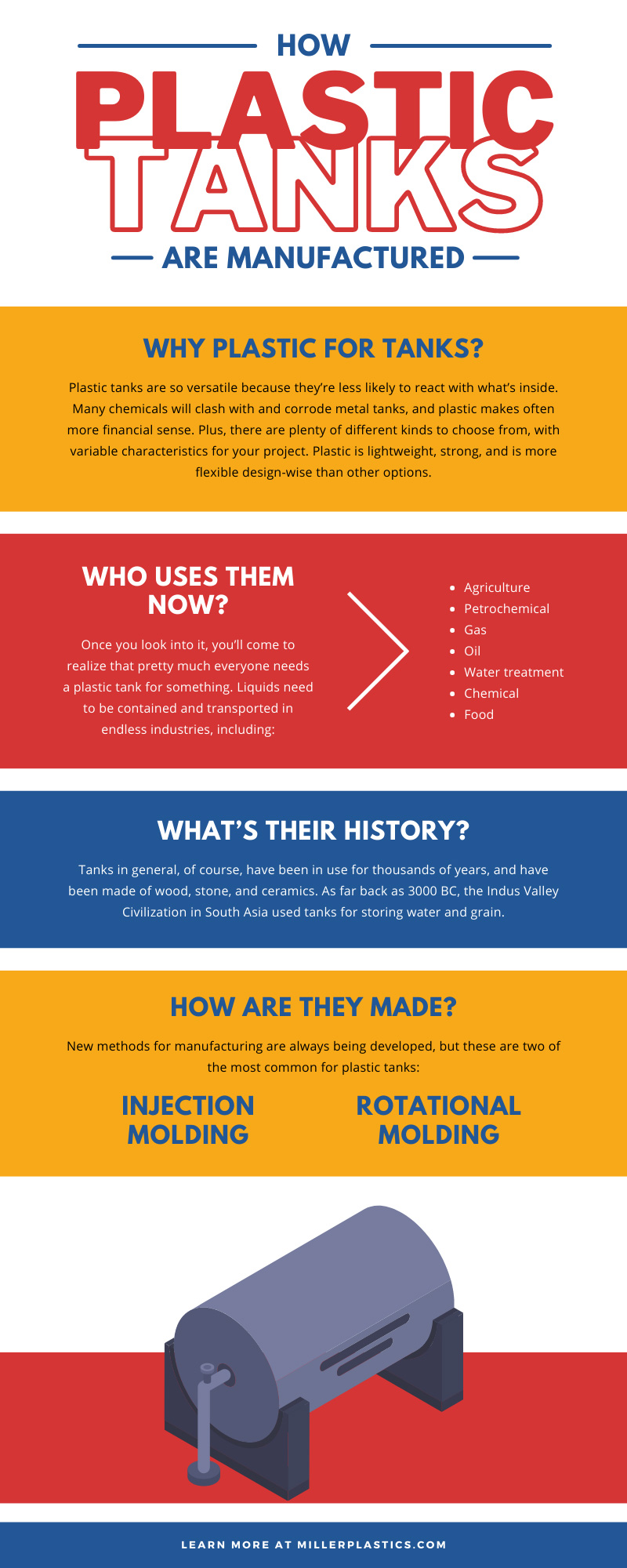